Beyond the high walls
Glimpse of the Colombo Dockyard:
by Nilma Dole and Imantha Caldera
How often have we wondered how the world was like beyond the walls of
the Colombo Dockyard. For the first time last week, we had the privilege
of discovering what was within this mysterious fence. Visiting the
Colombo Dockyard is not easy.
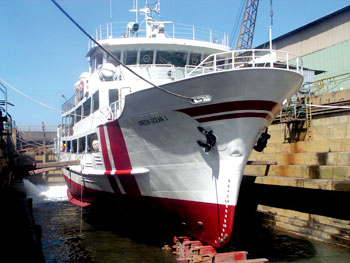
The Green Ocean |
After the process of authorising and checking ID cards a special pass
is given for those who want to venture inside. From the Dockyard Guest
House, we arrived at the Dockyard entrance and were taken to the
building near the Drydock 4 where the offices are located.
We went to the fourth floor of the conference hall for a presentation
where we met Darshana Chandrasekera the Marketing Manager of Ship
Repairs. We were told about the CDL history, processes and functions and
how it became a renowned name for ships to be built and repaired at the
Docks.
The Colombo Dockyard PLC (CDL) covering 11 hectares was built in 1906
during the British era and thereafter, it went to Sri Lankan hands after
independence. The CDL was privatised in 1993 after 51 per cent of the
shares was bought by Onomichi Dockyard Company of Japan.
Today, the CDL is a reputed name where many of the Maldives and
Indian ships call on the CDL port for repairs and many new ships are
developed.
The four areas that they focus on are: Ship Building, Ship Repairing
, Offshore Engineering , Heavy Engineering. Creating a new ship from
scratch is a Herculean task. Even though this is a tedious process and
takes a significant amount of time, CDL has created a good name in the
field because they deliver ships on time and within a good price.
This year, they already completed building the Great Ship Anjalie and
are building the Great Ship Amrita which both cost US$15 Million
respectively. These ships are part of a contract where four
anchor-handling tug vessels have to be created. In addition to this,
another two more Multi-Purpose Platform Supply Vessels need to be built
costing US$25 Million each.
CDL has orders till 2010 for building ships. Some of the ships built
by the CDL are: 65 Tonne Bollard Pull Berthing Tug , Ultra-Fast Crafts,
40 Metre Off-shore Petrol Vessels, 30 Metre Crew Boats, Fast-Landing
Crafts ,150 Passenger Vessels.
Every year 200 ships are repaired at the CDL. The Boshalis ship from
Maldives had a broken Bulbous Bow which is the 'nose' of the ship (where
the ship is directed to both sides) and CDL did a good job. Hull
repairing of many ships is what CDL mostly does. Vital jobs of ship
repairing is removing the rust from the outer plates which is called
Shot Blast. Shot Prime means giving a protective paint coating to the
ship.
Offshore Engineering is a field where CDL is keen on venturing into
where repairing of oil rigs is done. The offshore engineering area
creates profits but requires a lot of space if more developments have to
be made.
Heavy Engineering is land-based where major constructions like petro-chemical
and power station installations as well as heavy steel structures and
other specialised services (underground piping systems) are constructed
by the CDL.
Many cement blocks for roads are constructed by the CDL for the Road
Development Authority and chimneys are made for the Sapugaskanda project
and the Muthurajawella project. Gas tank constructions are also done
where many clients from Maldives have seen the work of CDL and have
assigned them to do their constructions as well.
The employees of the CDL consist of 1500 direct employees and 1500
who are on contract basis. They have their own radio channel to motivate
and inspire them while having free meals everyday. They make sure that
they complete the order according to the stipulated time.
The highlight of the familiarization tour was when we climbed onboard
the Green Ocean ship which was undergoing repairs at the CDL at the
time. Owned by Green Lanka, this 500-passenger-ship was formerly known
as the City of Trinco. Captain Somasiri showed us his ship which was a
passenger ship that ferried people from Trinco to KKS and vice versa.
The communication equipment and radio systems as well as engines and
powerhouses were shown to us.The yearly safety procedure check on
lifejackets and lifeboats was done as a result of this repair.
After being shown around the dockyard by the Marketing Manager of
Ship Repairing at the CDL Prince Lye, we returned finally having found
out what goes on beyond those high walls.
[email protected]
Do you know how a ship is built?
As you can imagine, it must be an enormous task to build a ship. The
first stage is cutting different parts from two metals namely steel and
aluminium. These metals are actually frames where various parts of ships
like the hull and keel are made from.
These frames are Shot Blast and Shot Primed. Shot Blast means
removing the rust from the metals and Shot Primed means painting a
smooth rust-free grey coat over the frame. The parts are cut by an
electrical optical flame cutter and folded into the shape of the ship's
body.
Afterwards, the parts are fitted and placed as a ship at the
construction site. The crane helps transport parts to make the ship. The
crane also lifts steel rods to make the ship and beams. Lots of Steel
and Aluminium parts are needed to make the ship strong and sturdy. The
inside parts like the engine and seats are also fitted.
Also, the wood made from teak helps build the deck of the ship which
is a vital element. Life jackets and life boats are also built which are
an integral part of the ship's safety procedures. Communication
equipment and various instruments are also installed. Lots of people in
the Dockyard work night and day ensuring that the ship is delivered on
time since business and profits are dependant on it.
The finishing touches include waxing and spraying the ship with
colour and a protective coating against rust and dirt. The new ship is
now ready for the first swim in the sea. |