Prospects increase for handwoven products:
Maruthamunai handloom products break new ground
by Naalir Jamaldeen
Maruthamunai is a beautiful village situated along the Eastern
coastal belt nearly five kilometres off Kalmunai City. Since 1932 the
people in this village produce handloom for the local community.
Maruthamunai sarongs were famous in Sri Lanka prior to the advent of
Indian sarongs. The tsunami severely affected the handloom industry in
Maruthamunai and Kalmunai.
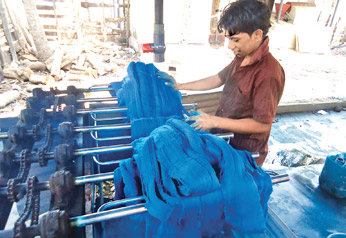 |
Material being
dyed |
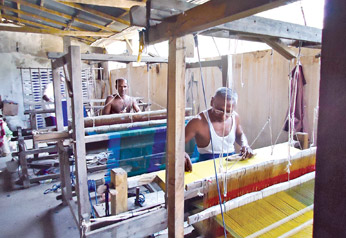 |
Two workers at
loom |
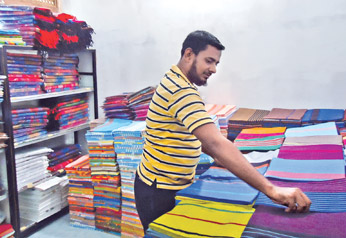 |
A worker
arranging the loomed saris |
Pix: Naalir
Jamaldeen |
A large number of looms was destroyed killing thousands of people
including experienced loom workers. Over 768 looms were destroyed,
Eastern Social Mobilising Organisation (ESMO) sources said.
Loom operators in the Kalmunai Divisional Secretariat experienced a
loss of over Rs. 6.8 million. According to ESMO, over 1,084 families in
the Maruthamunai produce handlooms. Skilled workers is the main problem
which the industry is currently undergoing.
We spoke to a cross section of loom operators. Ismail Lebbe Muhammad
Hassanar said that production cost of handlooms is high compared to
powerloom material but still top the market.
There is a shortage of workers in this sector after the tsunami. The
percentage of the younger generation who enter this industry is reducing
drastically due to the availability of opportunities for higher
education. Wages for loom workers are low compared to the wages from
other sectors such as carpentry and masonry and earn Rs. 1,000 per day,
Hassanar said.
He said that Rs. 140 is given to weave a metre of fabric. A worker
can weave from five to six metres of cloth per day.
Sarongs, shirts fabric, saris, table cloths, bed sheets and pillow
cases are produced at Hassanar’s loom. “Imported cotton thread is used
in the weaving process. Completed products are distributed to individual
shopkeepers in Kurunegala and other parts of the country. We also
receive orders from others including tourist hotels from time to time”,
Hassanar said.
Hassanar said that prior to the tsunami, over 21 people worked with
him, but now the number has dropped to seven. “Due to tsunami we
experienced a loss of Rs. 1.3 million”, Hassanar said.
Hassanar produced Dhamma school uniform materials before the tsunami.
Due to the shortage of experienced workers he said he was unable to
produce Dhamma school uniform materials any more. With a view to
improving the handloom industry in the region, he conducted a series of
workshops for youth in the region. Workshops were held in five places
including Thirukkovil and Satturukkondan.
He said that eventhough newcomers weave, the quality is not
satisfactory. No dealer is ready to purchase these products. Weavers
must be given incentives if the industry is to survive. It will take
time for new weavers to learn the art. Arrangements must also be made by
the relevant authorities to market their products.
Hassanar has undergone training in Norway. He has also been to India
to study techniques of handloom weaving.
Hassanar said that he was prepared to train the younger generation.
Handloom weaving is an independent industry. Weaving at loom is not
difficult. Even at homes looms can be operated. It can also be made a
hobby.
The finish in handloom textiles produced in Maruthamunai was
excellent when compared to textiles woven by powerlooms.
Powerlooms can produce over thousand of metres of cloth per day. But
the quality varies. There is a demand for Sri Lankan handloom textiles
in the world, Hassanar said. So it was necessary to teach the younger
generation to operate on handlooms.
There are nearly 18 professional and a large number of domestic
weavers in the Maruthamunai, according to Hassanar. He said that as this
was the off season, sales have decreased. Production and sale will
increase during festive seasons such as Sinhala and Hindu new year,
Ramadhan and Haj festivals.
There are two types of dye used in the dying process of thread
natural and artificial. Natural dyes are costly as lot of herbs are
included, Hassanar said.
Hassanar said that the Government had trained 15 handloom operators
to produce natural dye. Meanwhile, the weavers focused only on a few
items; by producing new varieties international market can be attracted.
There is a demand for Sri Lankan hand woven products in Norway. Beige
coloured products have a demand in Norway. There is a tendency among the
Norwegians that they will not change the colour choices from time to
time, Hassanar said. The authorities should import yarn to cater to the
international market. Local weavers must coordinate with the
international textile market and middlemen should be prevented from
being involved, he said. Hassanar said that the handloom operators have
also brought their problems to the attention of the Export Development
Board (EDB).
Hassanar has received two awards from the Ministry of Textiles for a
Salwar kit and a sari produced using the Petthampili technique. Muhammad
Ibrahim Ubaidul Rahman, Managing Director of Jahi Weavers said that over
150 families were working with him.
The Eastern Provincial Director of Industrial Development in
Trincomalee encouraged Rahman to start a people’s company, which he did,
with more than 300 people who had a history in weaving, pooling in small
amounts of money, and turning out a few sample products, they went to
Colombo, to meet the Director of the Department of textiles, Vijitha
Seneviratna. “The Textile Director was very happy”, said Rahman.
Rahman started his handloom industry with five looms in 1999, he was
able to increase the number of looms to 25 in 2001. He bought a land for
his industry with credit assistance from the EXPO centre. He gathered
groups of weavers and put up small cottages, placing in each, five looms
and one supervisor. Weavers could also weave at home and the work is
collected. “In one month about 3,000 sarongs, 1,500 saris, and other
materials were complete, Rahman said.
“Now customers come to Jahi Weavers from various parts of the country
such as Colombo, Kandy and Ratnapura to buy our products.
After the dawn of peace in the country the number of customers have
also increased by a considerable level. At present there are about 100
cottage factories and around 1,000 families involved in weaving. They
earn more than Rs. 700 per day,” Rahman said.
Rahman’s people’s company also holds regular exhibitions at the
B.M.I.C.H. receiving stalls and free transport service from the
Department of Textiles and linking with new suppliers. “In 2003, we had
the best ever exhibition. In three days, all our products were sold and
we collected Rs.2.5 million. Shop owners and individual buyers were
surprised that Sri Lankans could make such good quality products like
that,” Rahman said.
Since the duty on Indian materials has increased, Maruthamunai should
seize the opportunity to improve the handloom industry. Yarn for the
looms is imported from India by suppliers in Colombo at 20 percent
discount.
Rahman has a quality checking area. He has set up loom cottages in
Maruthamunai, Neelawanai, Navithanveli areas. “We have expanded this
upto Katthankudy and Eruvil”, he said.
Mainly Kurtha, blouse, ladies top, ladies pant materials, sarongs,
saris and wedding saris are produced at Rahman’s looms. Rahman receives
sari orders from textile owners in Colombo from time to time.
Over 500 metres of fabric is woven per day at these looms. A metre of
cloth material is sold from Rs.500 to Rs.600.
Rahman said that as a result of increase in the production cost,
their level of income has declined considerably. Weavers are unable to
increase the price very frequently. The change of dollar value has also
affected this industry.
Rahman targets the local customers. His products are available at
textile shops along Galle Road, Colombo.
Rahman said that there is a large number of experienced weavers in
Navithanveli and Thalangkuda areas. There is enough possibility for the
emergence of new weavers in the future from here. Rahman is operating
looms with the help of 15 experienced weavers in these areas. He also
plans to develop looms into a factory. Rahman has also made a request
from the authorities that the handloom weavers in Maruthamunai should be
entitled to benefits being provided by the Government.
Rahman is weaving silk materials on a mini scale. Workers have to be
trained to weave silk fabric. Now workers are being trained gradually.
Modifying the existing looms will help increase the production capacity
and quality. Rupees 50,000 is required to modify a single loom. He has
225 looms at present. Rupees five million will be required to modify all
looms.
Rahman maintains a separate plant for dyeing. As a large quantity of
yarn is dyed daily, there is the threat of environment pollution. So
Rahman plans to set up a waste water treatment plant at his factory
premises with a view to minimise environmental hazards.
He expressed confidence that the handloom industry can be modified to
cater to the needs of the present era. Handloom textiles have now turned
into luxury cloth material. We need advice and guidance from the
Government, he said.
Rahman said that he is importing yarn from India. Egyptian cotton is
the best in the world but it is very costly. Similar quality yarn is
available in India.
Rahman imports thread from Koyamputtur. There are enough choices. He
uses over 4,000 kilos of yarn every month. Meanwhile, Rahman has won the
first prize in the Eastern province for colour matching sari organised
by the Ministry of Textile Department.
He also won the second prize offered by the central Government.
The Government has given orders to weave Dhamma School saris with a
view to help handloom weavers. Rahman has also been given orders by the
Government to produce Dhamma School saris. |